Click to listen to this article
|
By Jared Gutierrez, Volm Companies
In today’s market, it’s fair to say that everyday pressures aren’t the exception but the norm. Employment costs, labor shortages, sustainability, inflation, production issues and so on are creating challenges far and wide. As with any complex situation, there’s no one-size-fits-all solution. But in both my roles as president of the National Onion Association and general manager of the Pasco, Washington, division at the Volm Companies, I can tell you that innovation is proving to be a sensible way forward.
Automation, in particular, has been a great way to proactively innovate while adapting to the changes we’re seeing in the market. These developments are particularly timely as we continue to see an industry-wide shift from bulk packaging to more consumer bags 10 pounds and under. But the costs involved here cannot be overlooked. Investing in research, development, sustainability and other efforts are all worthwhile endeavors. The reality, though, is that none of them come cheap.
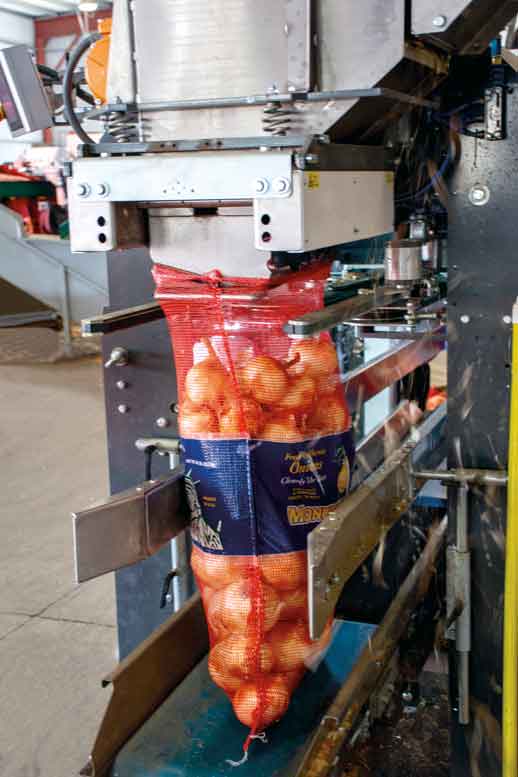
When it comes to automation, for example, growers and packers must make considerable, up-front investments in equipment, sufficiently train their employees and adequately maintain each piece of machinery. I’m not going to lie – there’s a brief moment of sticker shock. But I’m also going to tell you that once these initial growing pains are over, the return on investment is well worth the cost and effort. Consider businesses that have installed Volm’s MD series of weighers. Not only are these machines fast, but they are highly accurate. Sheds that have welcomed them into their equipment lines have been able to drastically cut down on expensive labor as well as significantly reduce their giveaway. So that initial investment is paying off in the present and will continue to do so in the foreseeable future.
Controlling Costs
Cost impacts are a critical factor on any given day, but they’re especially important now. We’ve all been feeling the pinch of inflation, and the rising cost of goods and services hasn’t been easy on anyone. Like many growers and packers, Volm knows what it’s like to feel squeezed by those cost pressures. And we also believe in managing our costs as best as possible. I truly feel that this is a shared responsibility. Growers, packers, suppliers, retailers and everyone else who plays a role in our food chain shares a responsibility to reduce waste, minimize inefficiencies and manage their dollars as responsibly as possible so that costs don’t simply get handed down to families sitting at the dinner table.
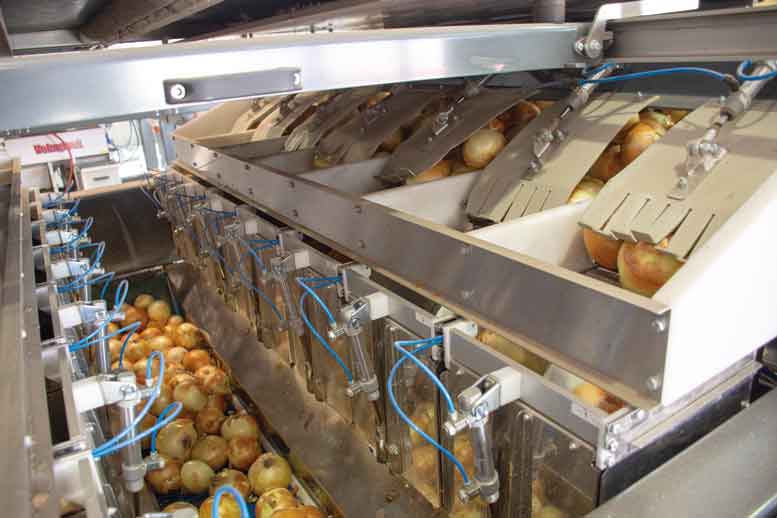
At Volm, we are doing our part in a number of ways, and this includes sourcing competitively, leveraging strategic partnerships and ensuring that our facilities are run as efficiently as possible. Recently, we started applying lean strategies to drive internal process improvements throughout the business. As a part of this, we’re identifying and eliminating waste in all forms with the intent of creating value for customers through reduced order processing times and improved quality. In Pasco, in particular, new processes were implemented to improve domestic Leno costing, lead times and delivery.
Adding Automation
It’s important for all of us to continue to make positive changes. In the Pacific Northwest, I’m seeing more and more growers and packers replacing costly, timely and demanding manual labor with quick and easy equipment solutions. These solutions include the Volmpack Wicket Bagger for all-mesh consumer bags, the AutoPack for larger Leno bags and the AutoMesh Baler for packing consumer bags into roll-stock Raschel mesh master bags.
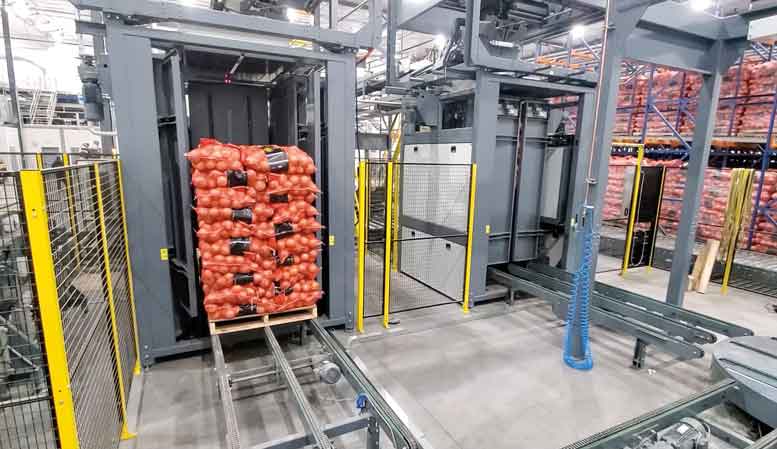
Equally exciting are some of the equipment solutions that have recently entered the market. The MoNo Clipper is a new clipping machine that demonstrates that less is more. That’s because the bag is made without a metal clip, eliminating the need for clipping wire.
Another standout addition is the BD808 Case Packer, which is a compact, high-speed and fully automated case packing system. Here, consumer bags are dropped into an intermediate chamber, where they are staged ahead of a final deposit into the master carton. Depending on the bag size and other variables, this method produces pack rates of up to 80-85 bags per minute.
Palletization is also an exciting area where we’re seeing tremendous benefits for the onion industry. This is because the latest generation of equipment solutions offers superior stacking quality, despite onions’ well-earned reputation of being a difficult-to-stack product. The latest palletizing solutions are highly adept at containing and compressing each layer. This method of palletization prevents shifting of product and successfully achieves a strong and sturdy stack.
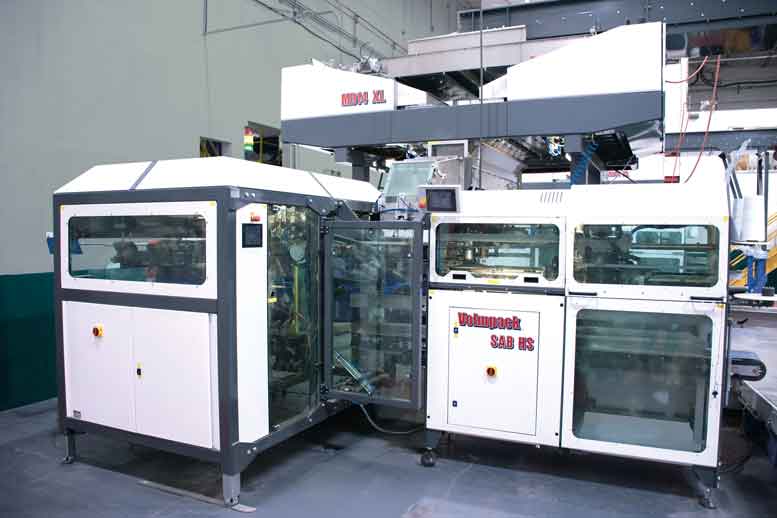
On packaging, there continues to be lots of interest in products that minimize waste and reduce our environmental impact. For onion packers, eco-friendly netting is available, including compostable knitted or extruded netting and lighter weight nets that use less raw material to produce. Also worth mentioning are the benefits of using all-mesh packaging, which allows for the breathability that onions need. Mesh helps to maintain a longer shelf life, which prevents unnecessary food waste. For bag closures, the CloseIt Bio-Clips are our more sustainable offering. This clip is biodegradable and contains 100% USDA certified bio-based content. Compostable wineglass labels are also an option.
The list of innovations entering the market gets more extensive all the time. And the good news is, as the industry continues to invest in the future, we can count on seeing more offerings down the road.
Predicting the future of the onion market is a bit like predicting the weather; there are never any guarantees. But one thing remains clear. If today’s challenges have taught us anything, it’s that businesses that innovate will continue to thrive today, tomorrow and beyond.
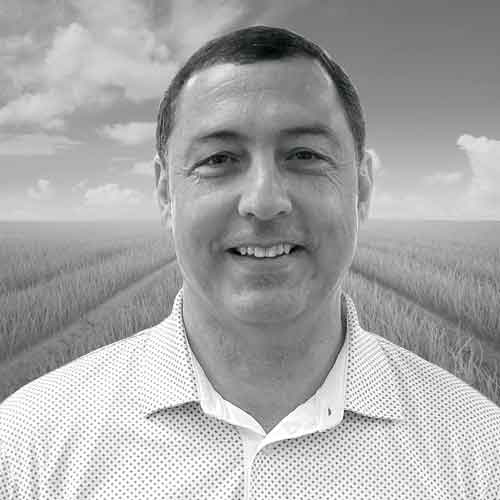