Click to listen to this article
|
By Nico Nieuwenhuize, Eqraft
Blue Sky Onions in Royal City, Washington, has taken automation and efficiency to new heights in the last few years. The onion grower and packer installed the first fully automated electronic grader from Eqraft on the West Coast and adopted the European method of grading and packing.
Owners of Blue Sky Onions took a leap of faith when they decided to skip the half measures and invest in automation across the board. Opting for a new electronic onion grader as well as a newly built packing shed featuring several weighing and packing machines, Blue Sky Onions is now one of Eqraft’s exemplary projects on the West Coast.
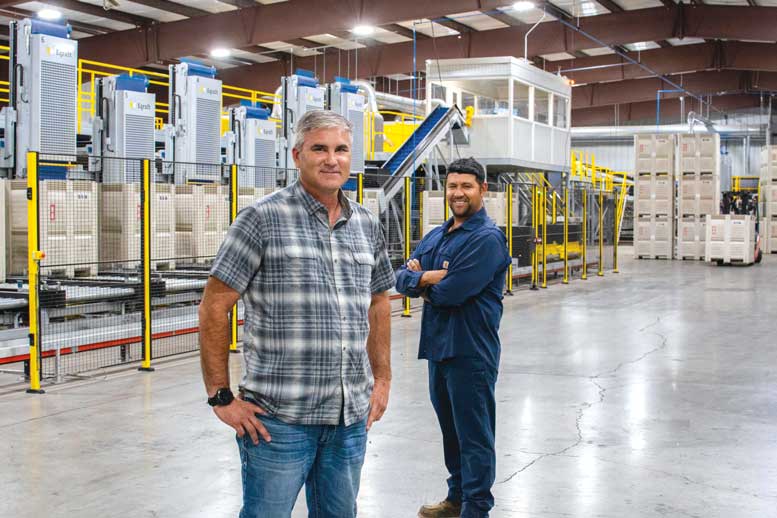
Family Farm
Blue Sky Onions is a family business, founded in the 1970s by Jake Wardenaar’s parents. The family moved to Royal City over 50 years ago and has been building a stable business ever since, growing and packing onions and shipping them to clients in the retail grocery and foodservice industry.
In addition to onions, the family business also grows potatoes, apples, cherries, alfalfa, green peas, corn and wheat. Blue Sky supplies its produce to the Basin Gold Cooperative, a group of growers and shippers that markets the onions. Wardenaar grew up on the farm but gained experience at another company for about eight years after college before joining his older brother, Joel, in the family business.
“I’m responsible for the onions, from grading to packing and selling. That also includes making strategic decisions such as investing in new equipment. My brother runs the farm operations of the onions and other crops,” Jake Wardenaar said.
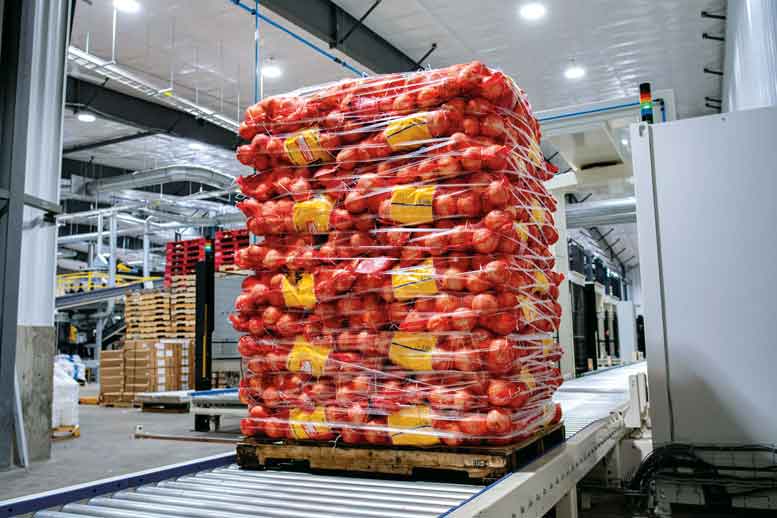
Clear Vision
The decision to purchase Eqraft’s electronic grader was years in the making, according to Wardenaar. With his family being of Dutch heritage, he has a personal connection to the Netherlands and has been visiting the country for years – both for business and pleasure. About seven years ago, he received an invitation from Eqraft for the first demonstration of the Eqrader optical onion sorting machine at HOZA in the Netherlands.
“I went and spoke to Eqraft about what I thought had to be done to make the technology work for our U.S. onions as well,” Wardenaar said, referring to the difference in onion size. Onions grown in the western U.S. are much larger than their European counterparts, requiring machinery and technology to be adapted.
In the years after that, he continued to follow the development of the onion grader. He even visited several reference projects in the Netherlands including the world’s largest automated onion processing line at MSP Onions, as well as Go Products, a smaller family business.
“During those trips, I got a good sense of what the Eqrader could do and how I wished to implement it in my own business,” he said. “When the time came to invest, I already had a clear vision on how we would do things, so the decisions were made fairly fast.”
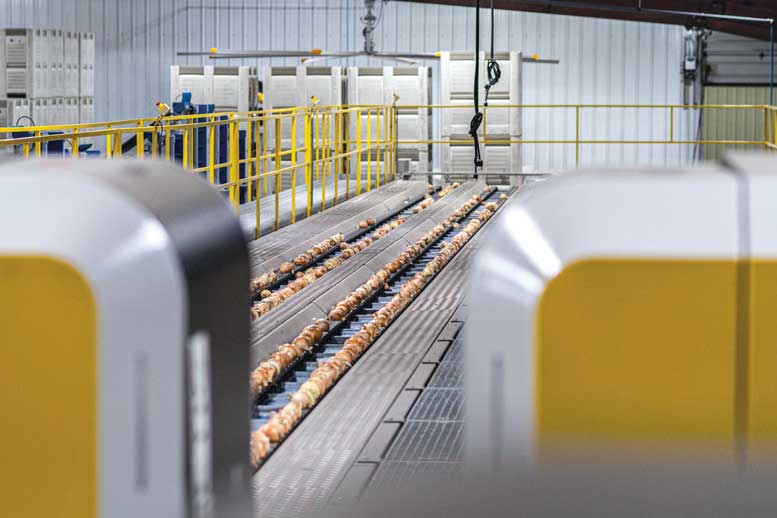
Against the Grain
In addition to investing in an optical grader, Blue Sky also built a brand-new shed for its new Eqraft packing line and adopted the European standard for packing. This means graded onions go into storage before they’re packed instead of sending them directly from the grader to the packing line, as is common in the U.S.
Many U.S.-based packers think it’s best to avoid the extra step of putting produce in storage first, but it’s actually the opposite, according to Mike Kooijman, technical sales executive at Eqraft.
“By putting the onions in bins and leaving them in storage for a little while, they are given time to heal before being packed and transported. We take gentle handling very seriously at every step of the process,” Kooijman said.
More importantly, having a storage with already graded onions in different categories benefits efficient packing.
“Before grading the onions, you don’t know exactly what you’re going to get out of a batch; you might need category A onions but end up with predominantly category B,” Kooijman said. “Taking fewer onions out of a batch than you anticipated means your packing machine can’t perform at full capacity, slowing the process down.”
“By packing a batch of onions you haven’t sold yet, you risk having to pack the batch again because the client prefers a different type of bag,” he added, explaining that having graded onions in storage allows the packing line to use its full capacity and increases flexibility, and that makes a difference on the factory floor. “We’re really happy with how quickly we are able to react to client orders now.”
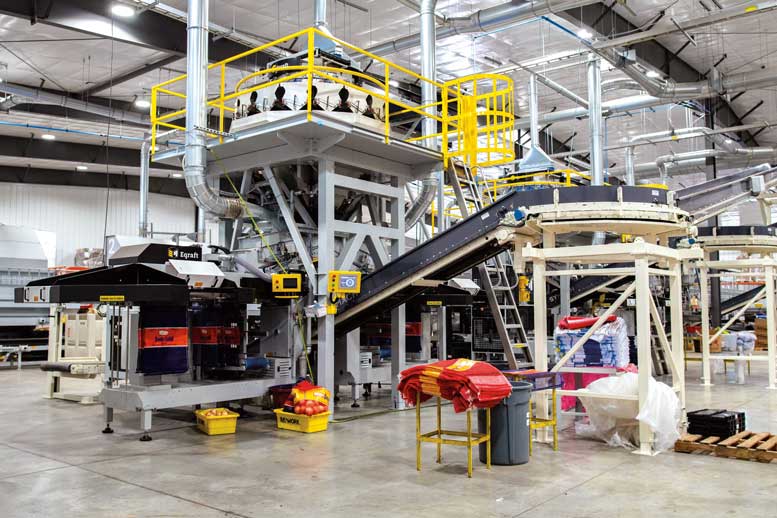
No More Heavy Lifting
After a trip to the Netherlands in the spring of 2022, Wardenaar signed on the project in the summer of that same year. Just before Christmas 2023, the new lines were up and running.
“We had to build the new packing shed, take care of the permitting process, install the new lines, get everything up and running, and learn how to work with the new equipment,” he said of that challenging first year.
Being the first Eqrader installation that processes West Coast onions, the machinery and technology had to be tweaked to fit a larger-sized product.
“Blue Sky took a leap of faith on us, and we’re grateful for that,” Kooijman said.
After working with the new line for over a year, Wardenaar said he’s glad he did it.
“With the Eqrader, we’ve added 50% more capacity compared to the previous situation. We’re very pleased with it, as we can now do a much better job in sorting out onions with skin discoloration and internal rot, and grade them accurately based on sizing,” he said. “Thanks to the level of automation, there are no jobs that require heavy lifting anymore. What’s left is just some light manual work, such as hanging bags onto the Baxmatic bagging machine. It’s a nice working environment for our crew.”
Wardenaar is glad he ultimately decided to opt for a complete new grading and packing line, investing in a new building as well as several machines that will help him face daily challenges for years to come.
“It was a risky endeavor because a large sum of money was involved,” he said. “But I think these types of long-term investments ultimately pay off.”
Like Eqraft, he believes in looking ahead and securing future-proof equipment for the coming decades.
“Instead of trying to solve an individual problem we’re facing today, I try to anticipate the problems we will encounter further down the line, investing in comprehensive solutions that will set us up for long-term success.”